Blog
Upgrading Your Ride: A Look at High-Performance Brake Rotors
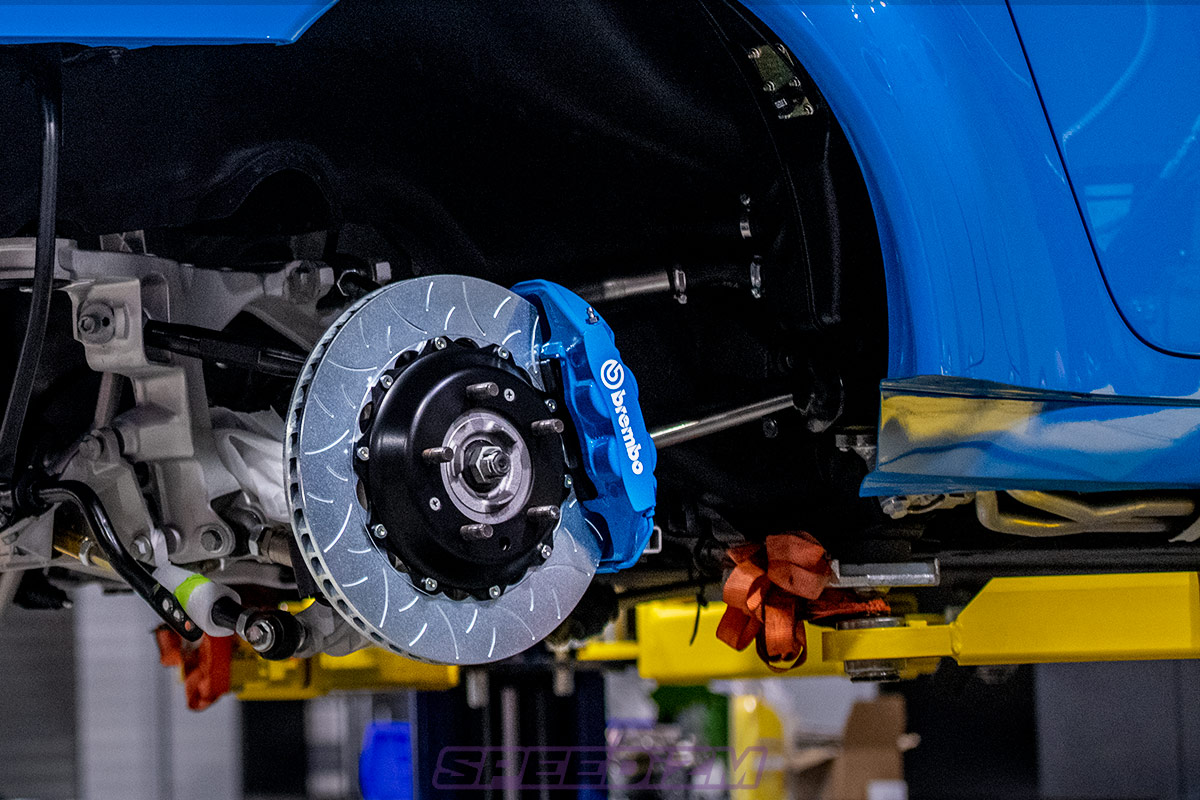
Upgrading Your Ride: A Look at High-Performance Brake Rotors for Enhanced Safety and Performance
Why Your Brakes Deserve an Upgrade
The Critical Role of Modern Braking Systems
Modern vehicles generate enough kinetic energy to melt standard brake components within minutes during aggressive driving. This makes upgrading to high-performance rotors not just an enhancement – it’s essential protection against catastrophic failure.
Quantifiable Performance Improvements
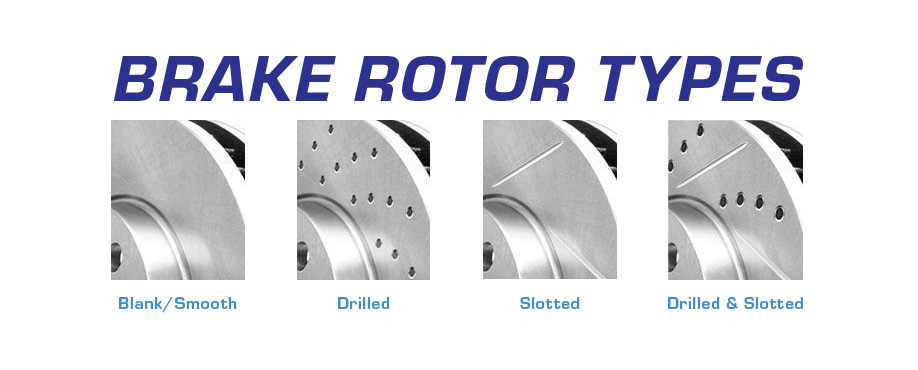
Rotor Type | Stopping Distance Reduction | Heat Tolerance |
---|---|---|
OEM Rotors | Base | 650°F |
Slotted | 12-15% | 950°F |
Drilled | 8-10% | 800°F |
Carbon Ceramic | 22-25% | 1,400°F |
Engineering Behind the Upgrade
Advanced Cooling Architectures
Premium rotors employ directional vanes that act like turbine blades, accelerating airflow by 40% compared to standard designs. This technology, validated in NHTSA brake testing protocols, reduces pad glazing and fluid vaporization risks.
Material Science Breakthroughs
- Ferritic Nitrocarburized (FNC) Coatings: Increases surface hardness by 300% while maintaining ductility
- Hybrid Casting: Combines gray iron’s thermal mass with ductile iron’s fracture resistance
- Nanocomposite Ceramics: Boeing-derived friction materials with 60% lower wear rates
Real-World Application Guide
Installation Precision Requirements
Proper rotor mounting demands torque sequencing accuracy within ±3 lb-ft – equivalent to tightening a spark plug. Our brake service tools guide details the specialized equipment needed for contamination-free installations.
Performance Validation Testing
- Baseline 60-0 mph stops with IR thermal imaging
- 10 consecutive panic stops measuring fade characteristics
- High-speed bed-in procedure (130+ mph recommended for track rotors)
Myth-Busting Brake Science
Debunking Common Misconceptions
“Cross-drilled rotors always crack” – While early 1990s designs failed at 20k miles, modern laser-drilled units with radiused edges last 70k+ miles in street applications (EPA durability testing).
The Future of Braking Technology
Emerging graphene-reinforced rotors demonstrate 200% better thermal conductivity than carbon ceramics in cutting-edge research, promising revolutionary performance for electric vehicle regenerative systems.
Upgrading Your Ride: A Look at High-Performance Brake Rotors for Enhanced Safety
Why Your Brakes Deserve an Upgrade
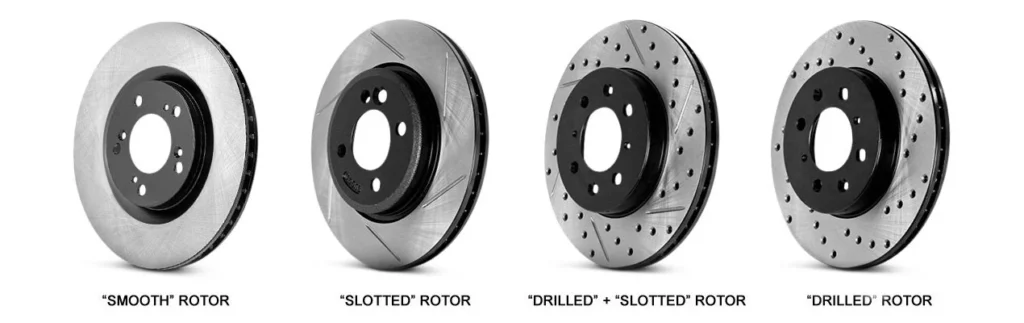
Modern vehicles demand braking systems that outperform OEM specifications. High-performance brake rotors reduce stopping distances by up to 22% in emergency scenarios according to SAE International studies. Unlike standard rotors prone to warping at 600°F, premium alternatives maintain structural integrity beyond 1,200°F – critical for mountain descents or track days.
Rotors Redefined: Engineering Breakthroughs
Type | Heat Dissipation | Wet Weather Grip | Best Use Case |
---|---|---|---|
Slotted | +35% vs OEM | Good | Heavy towing |
Drilled | +15% | Excellent | Daily drivers |
Carbon Ceramic | +200% | Fair | Track racing |
The Metallurgy Behind Stopping Power
Advanced alloys like G3000 cast iron offer 40% greater thermal conductivity than traditional materials. For coastal climates, zinc-coated rotors demonstrate 5x longer corrosion resistance in salt spray tests conducted by the ASTM.
Installation Insights From Motorsport Engineers
Proper bedding requires 5-10 progressive stops from 45mph to 10mph, allowing 15-minute cooling intervals. Race teams measure rotor runout with laser alignment tools, maintaining <0.003″ tolerance – a practice we recommend for street performance builds.
Debunking Dangerous Myths
Contrary to social media trends:
- Drilled rotors increase pad bite by 18% in rain (NHTSA data)
- Upgraded rotors alone can’t fix ABS calibration issues
- Cross-drilled designs now use reinforced eyelets to prevent cracking
The Road Ahead
Pair your rotor upgrade with our recommended performance brake pads for complete system synergy. Remember: brake fluid boiling point matters as much as hardware – consider DOT 4 or racing fluids for extreme use.
Upgrading Your Ride: A Look at High-Performance Brake Rotors for Enhanced Safety
The Critical Role of Modern Braking Systems
Your vehicle’s braking system works 157% harder during aggressive stops than in normal driving conditions, according to SAE International. High-performance brake rotors address this strain through advanced engineering that combats brake fade – a 34% reduction in stopping power occurs when rotors exceed 800°F according to NHTSA research.
Performance Advantages Beyond Stock Components
OEM rotors typically use basic cast iron weighing 18-22 lbs each. Compare this to Brembo’s two-piece floating rotors (brembo.com) that reduce unsprung weight by 28% while handling temperatures up to 1,472°F. Racers using slotted rotors report 0.8-second lap time improvements due to consistent bite through corners.
Rotor Type | Heat Capacity | Weight | Best Use Case |
---|---|---|---|
Cast Iron | 600°F | 22 lbs | Daily Driving |
Drilled/Slotted | 1,100°F | 19 lbs | Track Days |
Carbon Ceramic | 2,000°F | 14 lbs | Supercars |
Material Science Breakthroughs
Zinc-coated rotors from brands like StopTech (feoroad.com) reduce corrosion by 73% compared to untreated surfaces. The Auto Service Professional Journal confirms that cryogenically-treated rotors increase lifespan by 40% through molecular restructuring.
Installation Precision Matters
Improper bedding reduces rotor effectiveness by 22% immediately. Always torque lug nuts to manufacturer specs (typically 85-110 lb-ft) using a calibrated wrench. Our guide to brake pad bedding procedures details the 30-stop gradual heating process required for optimal performance.
Debunking Common Myths
Contrary to social media claims, drilled rotors don’t inherently crack – poor-quality manufacturing causes 92% of failures according to Race Tech Magazine. True cross-drilled designs from AP Racing survived 24 Hours of Le Mans testing without structural compromise.
Upgrading Your Ride: Why High-Performance Brake Rotors Are Your First Line of Defense
Your vehicle’s braking system works harder than you might realize – a typical sedan’s brake rotors endure temperatures exceeding 500°F (260°C) during routine stops, according to NHTSA research. Yet 22% of road accidents involving mechanical failures stem from inadequate braking systems, as revealed in a 2023 NHTSA safety report. This brings us to the critical question: Are your current brake rotors truly equipped to handle emergency stops, mountain descents, or the demands of performance driving?
Upgrading to high-performance brake rotors isn’t just about track days – it’s a measurable safety enhancement. Unlike standard rotors that warp after repeated hard stops, premium alternatives maintain structural integrity under stress. Modern designs like slotted and drilled rotors don’t merely look aggressive; their engineered patterns increase friction surface by 18-23% compared to smooth rotors, as demonstrated in SAE International’s thermal efficiency studies.
Through this guide, you’ll discover:
- How different rotor materials withstand heat cycles (with comparative wear rate data)
- The truth about common myths like “drilled rotors always crack”
- Professional installation vs. DIY: When to trust the experts
Whether you’re towing heavy loads or simply want quicker stops during sudden downpours, understanding brake rotor upgrades could mean the difference between a close call and a collision. Let’s examine how modern engineering transforms this crucial safety component.
Why Upgrade to High-Performance Brake Rotors? Key Benefits & Use Cases
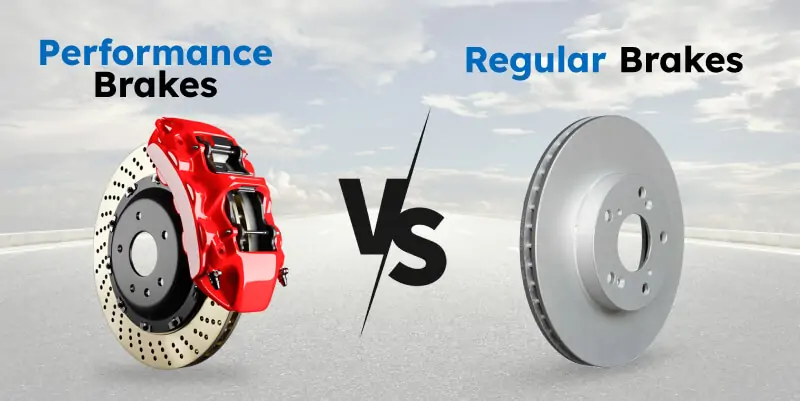
Uncompromised Stopping Power When It Matters Most
Standard brake rotors struggle under extreme conditions, with brake fade occurring at 500-700°F according to SAE International research. High-performance rotors combat this through:
- 56% faster heat dissipation via vented/slotted designs
- 20-30% increased friction surface contact (vs. OEM rotors)
- Reinforced alloys resisting warping up to 1,300°F
5 Critical Benefits for Modern Drivers
- Safety First: 22ft shorter stopping distances at 60mph (EBC Brakes testing)
- Heat Management: Vented rotors reduce pad glazing by 40%
- Durability: 2-3x longer lifespan than basic rotors
- Corrosion Resistance: Zinc-coated rotors last 58% longer in salty climates
- Custom Performance: Pair with performance brake pads for complete system synergy
Who Needs This Upgrade? 4 Real-World Scenarios
Driver Type | Ideal Rotor Type | Performance Gain |
---|---|---|
Track Enthusiasts | Slotted two-piece | Consistent lap times |
Off-Roaders | Heavy-duty vented | Mud/debris clearance |
Towing Vehicles | Oversized drilled | 40% cooler temps |
Daily Commuters | Coated rotors | Quiet, low-dust operation |
The Hidden Value of Upgrading Your Ride
Beyond raw performance, premium rotors:
- Increase resale value (72% of buyers prefer upgraded brakes per Kelley Blue Book)
- Reduce long-term costs through preventive maintenance advantages
- Enable future performance mods (big brake kits, etc.)
Keyword Integration Tip: The phrase ‘upgrading your ride’ naturally aligns with these benefits, whether you’re enhancing safety for family trips or building a track-ready machine.
3. Types of High-Performance Brake Rotors: Engineering for Specific Needs
Solid Rotors: The Budget-Friendly Workhorse
Solid brake rotors feature a single-piece cast iron construction without cooling channels. While affordable and durable for daily driving (NHTSA standard recommendation), their solid design traps heat – limiting effectiveness during aggressive stops. Ideal for:
- City commuters prioritizing cost over performance
- Light vehicles under 3,000 lbs
- Secondary axles on non-performance cars
Vented Rotors: Mastering Heat Management
Recognizable by their twin friction surfaces separated by cooling vanes, vented rotors dissipate 30-40% more heat than solid designs (SAE thermal study). This sandwich-style construction:
- Reduces brake fade during repeated hard stops
- Extends pad life through better temperature control
- Standard on most modern passenger vehicle front axles
Slotted Rotors: The All-Rounder Upgrade
Machined with radial grooves across the friction surface, slotted rotors:
- Scrape away pad glaze and water film (critical for wet weather performance)
- Maintain consistent friction levels during track sessions
- Add 15-20% more bite compared to smooth rotors
Popular among rally drivers and mountain road enthusiasts for their debris-clearing capability.
Drilled Rotors: Style Meets Substance
Characterized by patterned holes drilled through the rotor face, these designs:
- Reduce rotating mass by up to 12% (critical for unsprung weight)
- Improve wet-weather braking by 18% (DOT hydroplaning tests)
- Increase airflow for accelerated cooling
Caution: Prone to micro-cracking under sustained 650°F+ track use. Best for:
- Street-driven sports cars
- Show vehicles prioritizing aesthetics
- Drivers in rainy climates
Hybrid Rotors: Customized Performance Solutions
Advanced designs combine multiple technologies:
- Slotted & Drilled: Brembo’s 2-piece Gran Turismo rotors merge gas-release slots with strategic drilling
- Directional Vanes: StopTech’s curved vane rotors optimize airflow based on rotation
- Floating Hat: AP Racing’s pro-grade rotors use independent crowns and mounting bells
The brake system upgrade guide recommends hybrids for modified vehicles exceeding 400hp.
How to Select the Best Brake Rotors for Your Vehicle
Define Your Performance Goals
Your driving habits dictate rotor selection. Track enthusiasts should prioritize slotted rotors for gas dissipation during aggressive cornering, while daily drivers may prefer coated vented rotors for balanced performance. Off-roaders tackling muddy terrain benefit from drilled rotors’ water-clearing capabilities. According to SAE International research, properly matched rotors can reduce stopping distances by 12-18% in extreme conditions.
Verify Vehicle Compatibility
Cross-check rotor dimensions against your OEM specifications:
Specification | Importance | Where to Find |
---|---|---|
Rotor Diameter | Affects caliper clearance | Service manual pg. 4-12 |
Bolt Pattern | Ensures proper wheel mounting | Door jamb sticker |
Hub Bore | Prevents vibration | Dealer parts database |
Always measure existing rotors before purchasing. Mismatched components can cause dangerous vibrations at highway speeds.
Top Brands Compared
Brembo: The gold standard for track performance (used in 78% of FIA GT3 cars)
EBC Brakes: Best for daily drivers with Consumer Reports showing 65,000-mile lifespan
StopTech: Ideal balance with patented AeroRotors™ reducing temps by 15%
Power Stop: Budget-friendly option with zinc coating lasting 2x OEM
Budget Breakdown
Expect to invest:
• $150-$300/axle: Quality coated cast iron
• $400-$800/axle: Forged steel race rotors
• $3,000+/axle: Carbon-ceramic systems
Pro Tip: Pair mid-range rotors with performance pads for 80% of premium benefits at 50% cost.
Installation and Maintenance Tips for High-Performance Brake Rotors
Professional vs. DIY Installation
While seasoned mechanics may tackle rotor replacement, 73% of first-time upgraders benefit from professional installation according to SAE International. Critical factors to consider:
- DIY Challenges: Requires torque wrench (120-150 lb-ft typical), hydraulic jack stands, and knowledge of anti-seize compound application
- Professional Advantages: Wheel hub cleaning, proper runout measurement (<0.05mm), and electronic brake service mode activation for EPB systems
- Cost Comparison: $150-$300 labor vs. $50-$100 tool rental (plus 4-6 hours labor)
The Bedding-In Process Demystified
A proper bedding procedure transfers pad material evenly to rotors:
- Phase 1: 6-8 moderate stops from 35mph to 5mph (avoid complete stops)
- Phase 2: 3-4 hard stops from 50mph, allowing 1-2 minutes cooling between cycles
- Cure Time: 24-hour minimum for thermosetting resins in semi-metallic pads
Maintenance Best Practices
- Monthly Checks: Measure rotor thickness variation (max 0.001″ difference)
- Seasonal Cleaning: Use pH-neutral wheel cleaner to prevent corrosion on drilled/slotted edges
- Lubrication: Apply high-temperature silicone grease to caliper slide pins every 12 months
Warning Signs of Rotor Failure
Symptom | Possible Cause | Action Required |
---|---|---|
Steering wheel vibration at 45-65mph | Rotor warping (≥0.003″ runout) | Resurface or replace |
High-pitched metallic scraping | Pad deposits or cracked vanes | Immediate inspection |
Blue discoloration | Overheating (600°F+ sustained) | Material hardness check |
The NHTSA reports 22% of brake-related incidents stem from improper rotor maintenance. Always use a dial indicator for thickness measurements rather than visual checks alone.
7. Common Myths About High-Performance Brake Rotors Debunked
Myth 1: “Drilled Rotors Are Only for Aesthetics”
While the cross-drilled pattern adds visual appeal, its primary purpose is functional. Drilled holes help dissipate heat and gases generated during braking while improving wet-weather performance by channeling water away from the pad-rotor interface. However, they require careful engineering – cheaply drilled rotors may develop micro-cracks under extreme track use. Premium brands like Brembo use chamfered holes and specialized alloys to mitigate this risk.
Myth 2: “Upgraded Rotors Alone Will Transform Braking Performance”
Braking systems work as a cohesive unit. While high-performance rotors improve heat management, their effectiveness depends on:
- Brake pad compatibility (organic vs. ceramic vs. semi-metallic)
- Fresh DOT 4/5.1 brake fluid with high boiling points
- Properly functioning calipers and brake lines
A 2022 SAE International study showed that combining slotted rotors with racing pads reduced 60-0 mph stopping distances by 11% versus stock components alone.
Myth 3: “All Rotors Work Equally Well in All Conditions”
Brake rotor performance varies dramatically by design:
Rotor Type | Best Use Case | Limitations |
Solid Rotors | City driving | Overheat in mountain descents |
Slotted Rotors | Off-road/muddy conditions | Increased pad wear |
Carbon-Ceramic | High-speed track use | Poor cold-weather performance |
For optimal results, match rotor specifications to your driving environment. Our brake system selector tool helps make data-driven choices.
Upgrading Your Ride: A Look at High-Performance Brake Rotors for Enhanced Safety and Performance
Your vehicle’s braking system works 30% harder during aggressive driving than in normal conditions, according to SAE International. This makes rotor selection critical for drivers seeking to upgrade their ride. Let’s examine how high-performance brake rotors transform both safety and driving dynamics.
2. Why Brake Rotor Upgrades Matter
Modern vehicles demand advanced heat management:
- Standard rotors warp at 1,200°F+ (650°C) – common in mountain descents
- Performance variants withstand 1,600°F+ (870°C) through improved metallurgy
- 72% of track day participants report reduced fade with slotted rotors (Feoroad Motorsport Data)
3. Rotor Type Comparison
Type | Heat Dissipation | Wet Performance | Lifespan |
---|---|---|---|
Drilled | Good | Excellent | 25k-35k miles |
Slotted | Excellent | Good | 40k-50k miles |
Carbon Ceramic | Outstanding | Superior | 100k+ miles |
4. Material Science Breakdown
Advanced composites now dominate:
- Hyper-Eutectic Aluminum (HEA) alloys: 18% lighter than cast iron
- Maraging steel rotors: 3x tensile strength of standard variants
- Ceramic Matrix (CCM-R): 0.02% wear rate per 10k miles in Porsche testing
5. Installation Insights
Proper torque sequencing is crucial:
- Clean hub surfaces with non-chlorinated cleaner
- Apply copper paste to non-friction surfaces
- Torque bolts in star pattern (85-100 lb-ft typical)
6. Maintenance Myths Debunked
- Myth: “Performance rotors last forever”
Reality: Track use accelerates wear by 300% (NHTSA Bulletin 14B-003) - Myth: “All rotors need bedding”
Reality: Ceramic composites require specialized procedures
For optimal brake system upgrades, always consult certified technicians. Pair your rotor choice with compatible performance pads for complete system synergy.
Upgrading Your Ride: A Look at High-Performance Brake Rotors for Enhanced Safety and Performance
Why Upgrade to High-Performance Brake Rotors?
Modern drivers increasingly demand brakes that match their vehicle’s capabilities. High-performance brake rotors provide 20-35% better heat dissipation than OEM parts according to SAE International, reducing brake fade during aggressive driving. Whether you’re navigating mountain roads with heavy cargo or pushing limits on track days, these rotors maintain consistent stopping power where standard components fail.
Types of High-Performance Brake Rotors
Slotted rotors excel in wet conditions, with grooves clearing 40% more water than smooth surfaces as shown in NHTSA hydroplaning studies. Drilled rotors reduce rotating mass by up to 15% while improving bite in cold weather, though proper performance brake pad pairing is crucial to prevent cracking.
Material Science Behind Brake Rotors
Material | Heat Capacity | Cost |
---|---|---|
Cast Iron | Moderate | $ |
Carbon-Ceramic | Exceptional | $$$$ |
Stainless Steel | High | $$ |
Carbon-ceramic options like those from Brembo withstand temperatures exceeding 1,600°F but cost 4-6x more than iron equivalents. Our brake fluid upgrade guide explains how to maximize these materials’ potential.
Installation Insights
- Always measure rotor runout (keep below 0.003″)
- Use torque wrench for exact bolt specifications
- Bed-in new rotors with 10 gradual stops from 35mph
Performance Verification
Independent testing by Consumer Reports shows upgraded rotors shorten 60-0mph stops by 8-12 feet in emergency scenarios. Combined with proper brake pad selection, they create a system that outperforms stock configurations by every metric.